What are Wave Solder Pallets?
Wave solder pallets are a special type of fixture used during the wave soldering process to mask selected areas of the printed circuit boards that require thermal or solder protection. The masked areas usually contain SMT components, ground planes, gold fingers and/or mounting holes.
BENEFITS OF USING WAVE SOLDER PALLETS
- Protect heat-sensitive components.
- Improve solder flow.
- Eliminate solder skipping
- Eliminates hand masking.
- Reduces board warping.
- Reduces soldering defects and rework
THE WAVE SOLDERING PROCESS
Wave soldering is a process widely used in electronic manufacturing for soldering printed circuit boards with many through-hole components. It involves the use of a wave soldering machine. Circuit boards are placed on a conveyor system that traverses the entire machine. Please refer to the following image.
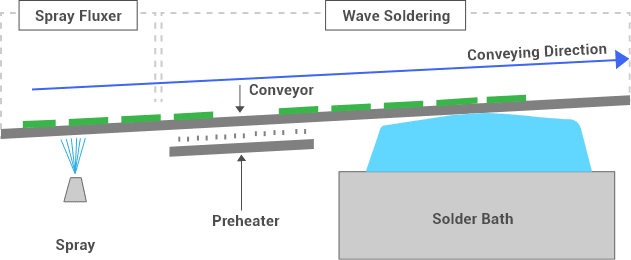
The process involves three main steps: fluxing, preheating, and soldering.
• In the fluxing stage, a flux material is applied to the surface of the printed circuit board to remove any oxidation or contaminants from the metal surfaces to be soldered.
• In the preheating stage, the printed circuit board is heated to prepare the surface for the soldering stage, where the board is passed over a wave of molten solder.
• In the soldering stage, the printed circuit board passes over the molten solder wave, the solder adheres to the exposed metal surfaces, creating a permanent bond.
Some wave soldering machines include a cooling chamber where the boards are cooled down to room temperature.
Wave soldering is an efficient and economical way to solder many components onto a circuit board at once. The solder joints produced through this process are very reliable both electrically and mechanically.
WAVE SOLDER PALLET FABRICATION
Wave solder pallets are fabricated with heavy-duty Electro-Static Discharge (ESD) composite materials such as Durostone® and Ricocel. These materials exhibit good machinability and can withstand the high temperatures and the chemicals associated with soldering applications.
The fabrication mainly consists of removing (with a CNC milling machine) material from areas of the pallets where the circuit board is to be exposed to the wave, and solder is required.
The design of a wave solder pallet can vary depending on the specific needs of the PCB and components being soldered, but in general, there are several key components that are commonly included:
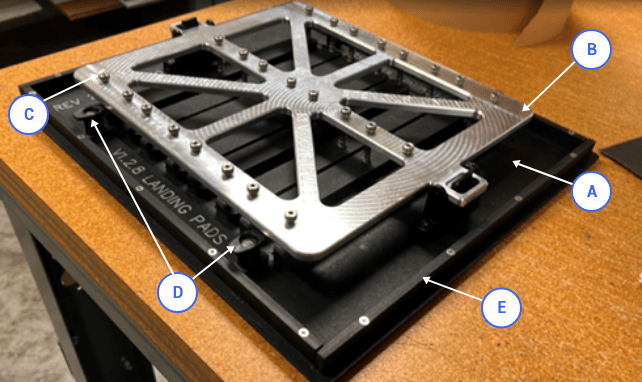
A) Base plate: Also known as base pallet serves as the foundation for the pallet and provides a flat surface for the PCB to rest on during soldering. It typically features cutouts and openings that allow the solder to flow through and create the necessary solder joints, while protecting the components from being damaged.
B) Top hat: Also known as Cover Plate, is designed to hold the components in place during wave soldering and sits on top of the Base Plate. It typically features openings to reduce weight.
C) Alignment dowels: They are used to ensure the Top Hat is correctly positioned above the PCBs.
D) Hold downs: They hold the PCB securely in place. They are commonly made of titanium and plastic instead of steel to avoid cross contamination.
E) Stiffener Bars – They are used to provide support to the pallet to reduce twisting and bending. They also prevent solder from going over the top area of the pallet.
F) Gas relief: Also known as vent holes are indentations on the pallet to allow gases to escape during soldering. They also help to prevent defects such as solder voids or insufficient wetting, which can occur when gases become trapped in the solder joint.
WHAT FILES DO YOU NEED TO PROVIDE?
Please provide the following files:
a. Gerber or DXF files
b. Step files
c. Photos of previously assembled boards (if available)
d. Special instructions
With Stencils Unlimited you do not have to wait for a quote. You can quote and order your wave solder pallet online or you can also request a traditional custom quote.